Snowman
Well-Known Member
There is a saying that goes: "The enemy of the good is the better," and in this case it might apply to solutions to your problems. As in "the enemy of the good solution (messing around with the flangeway tolerances) is the better...the easier...and that would be to overweight the cars and locomotives both. Perhaps to several times over the NMRA standard, in fact. The [HO] La Mesa MRR club does exactly this--a hundred car train might weigh 50 lbs (!) , which goes a long, long way to minimizing or even eliminating derailments.
I'm going to go out on a limb here (please don't take offense) and guess that if the problems are with off the shelf, rather than handlaid turnouts, then the train lengths are quite a bit shorter than 100 cars...in which case weighting the cars well over NMRA standard is probably a much simpler solution. Moreover, the heavy cars LOOK a lot better too--there is a perceptible feel of weight and inertia to all the cars...or the ones you overweight anyway.
I'll opine further: If flangeway depth is really a problem, then do be aware there is a tradeoff in which all the wheels might ride along the bottom of the flanges, but at the expense of the some of the treads riding too high, and thereby failing to make contact with the rails (which can also exacerbate the problems you are battling). Treads riding up and off the rails can also create electrical problems, as regards simple things like power to a locomotive--if the gaps are wide enough, the wheelsets might not make contact to draw power, resulting in stutter.
There can be similar problems with regard to track detector/detection circuits
Unless you are willing to start milling or turning wheelsets to tighter tolerances, it's certainly simpler to use whatever RP25 wheelsets you can buy off the shelf. Perhaps sort them, measure them, and discard the ones that are just too "rough."
There is also the old adage: "Don't reinvent the wheel," and in this case I'll point you toward "Proto: 87," a tighter standard, who's adherents have probably already battled through these problems and found workable solutions. You might peruse what they have already done, and follow their suggestions.
In any case, I wish you good luck battling the problems, however you choose to do it.
proto87.org
Good places to start, perhaps.
I'm going to go out on a limb here (please don't take offense) and guess that if the problems are with off the shelf, rather than handlaid turnouts, then the train lengths are quite a bit shorter than 100 cars...in which case weighting the cars well over NMRA standard is probably a much simpler solution. Moreover, the heavy cars LOOK a lot better too--there is a perceptible feel of weight and inertia to all the cars...or the ones you overweight anyway.
I'll opine further: If flangeway depth is really a problem, then do be aware there is a tradeoff in which all the wheels might ride along the bottom of the flanges, but at the expense of the some of the treads riding too high, and thereby failing to make contact with the rails (which can also exacerbate the problems you are battling). Treads riding up and off the rails can also create electrical problems, as regards simple things like power to a locomotive--if the gaps are wide enough, the wheelsets might not make contact to draw power, resulting in stutter.
There can be similar problems with regard to track detector/detection circuits
Unless you are willing to start milling or turning wheelsets to tighter tolerances, it's certainly simpler to use whatever RP25 wheelsets you can buy off the shelf. Perhaps sort them, measure them, and discard the ones that are just too "rough."
There is also the old adage: "Don't reinvent the wheel," and in this case I'll point you toward "Proto: 87," a tighter standard, who's adherents have probably already battled through these problems and found workable solutions. You might peruse what they have already done, and follow their suggestions.
In any case, I wish you good luck battling the problems, however you choose to do it.
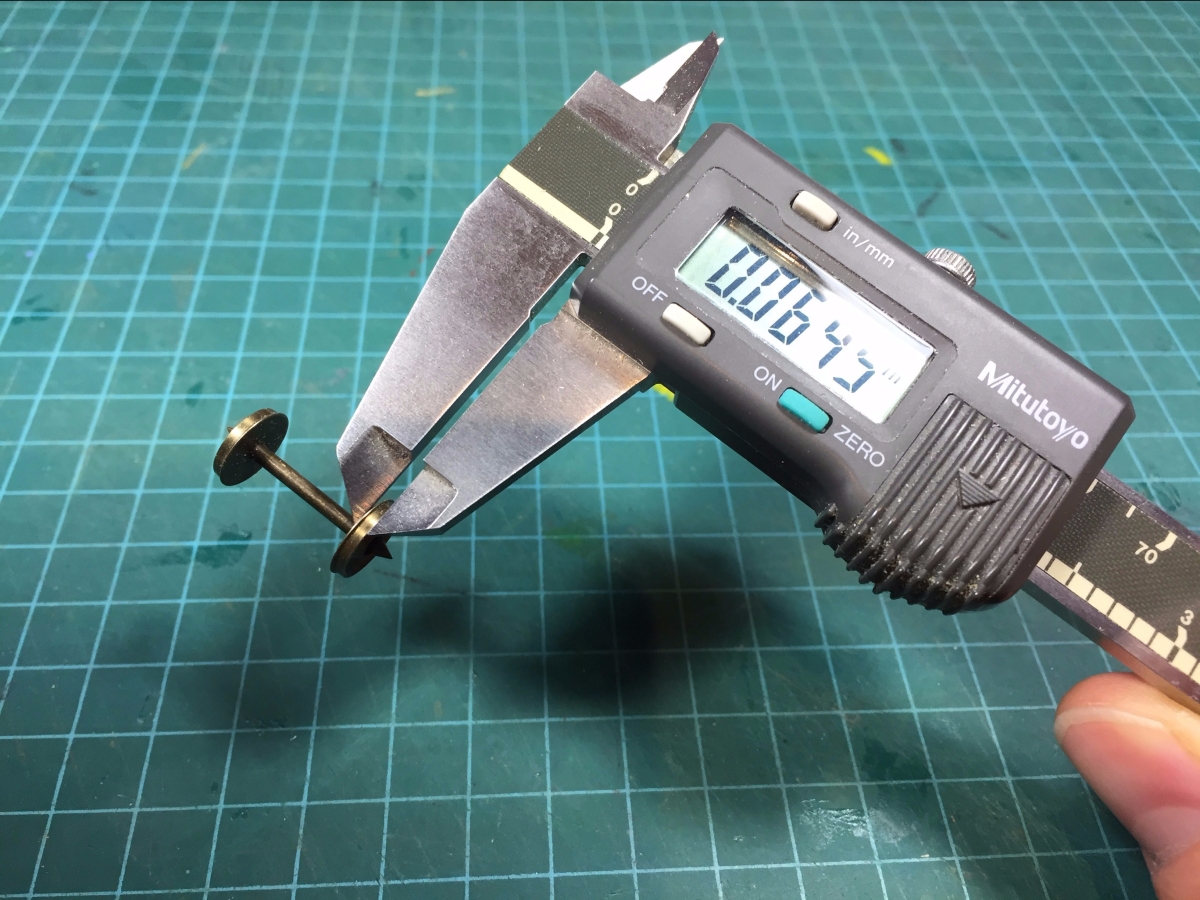
Standards
Wheels Back to Back (B) Tyre Width(N) Flange Width(F) Flange Depth(D) Wheel Check (K) Min Max Min Max Min Max Min Max Max Proto inch .611 .611 .063 .063 .013 .016 .016 .016 mm 15.52 15.52 1.61 1.61…
Good places to start, perhaps.
Last edited: